Features of the iDS® Series
The Advanced Coating System iDS® series makes possible low-cost, short-cycle coating processing (compared to our conventional products) by improving the performance of each component.
In addition, it is a next-generation arc ion plating Machine that can be install a sputter evaporator or other plasma source by a rectangular flange.
Short Cycle
iDS® Series has optimized pumping conductance and shortens cycle time compared to conventional systems because it greatly improves pumping speed.
Multi-element composite film performance
iDS® series has the optimum gear ratio for rotary tables, and can form a uniform multi-element metal nitride film any face of round-bar workpieces.
Versatile Expandability
iDS® series has rectangular flanges, which makes possible to mount a variety of plasma sources such as Steer One evaporator, conventional evaporation sources, and sputter evaporation sources.
Low running cost
Steer One evaporator has a rotating magnet mechanism that controls the arc spot.
As a result, the cathode cost can be reduced by uniform consumption.
Maintainability
Large front and rear doors facilitate maintenance access inside the chamber.
Operability
Fully automated processing by one touch.
(Operation check ⇒ Vacuum exhaust ⇒ Coating ⇒ Cooling ⇒ Atmospheric vent)
iDS® series common concept
The iDS® series is the next generation arc ion plating machine.
It has high-performance components, and has make possible an unprecedented low cost and short cycle coating process (compared to our conventional systems).
In addition it has a rectangular flange to install sputter and other plasma sources.
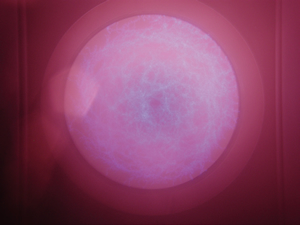
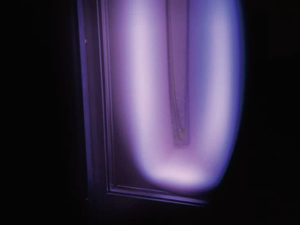
Steer one Evaporator
Steer one evaporator has a φ160 size cathode, and by forcibly scanning the arc spot with a unique magnetic field layout and motor-driven magnetic field rotation, it is possible to consume the cathode over a wide range.
Steer one evaporator has a 23% higher coating rate under the same conditions, and is compatible with a wide radiation angle, making possible to cover a wide coating area. (Compared with our conventional evaporation source)
In addition, Steer one evaporator has achieved a dramatic improvement in surface roughness. This is because the rotation of the magnet sweeps the arc spot, which reduces droplets.
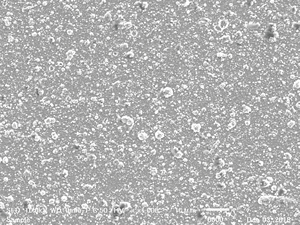
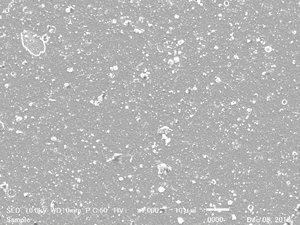
iDS® series lineup and Standard Specifications
iDS-mini | iDS-500 | iDS-720 | iDS-1000 | |
---|---|---|---|---|
![]() |
![]() |
![]() |
![]() |
|
Recommendation coating zone | (one evaporator type)φ450×H180[mm] (two evaporators type)φ450×H420[mm] |
φ500×H500[mm] | φ720×H800[mm] | φ1000×H1000[mm] |
Number of Arc Evaporator | 3 units or 6 units | 9 units (standard), 12 units (max.) | 12units (standard) | 12units(expandable) |
attached fixture table | 6-axis rotation fixture | 8-axis revolution fixture | 12-axis revolution fixture | 14-axis revolution fixture |
Coating method | Cathode arc ion plating | |||
Substrate etching method | Gas Bombardment, Metal Bombardment | |||
Arc Evaporator Unit | 2S Evaporator, Steer One Evaporator, Sputter Evaporator | |||
Recommended installation space | W3500×D5200×H3000 [mm] | W5500×D6300×H3000 [mm] | W4500×D7000×H3000 [mm] | W6500×D8500×H3000 [mm] |
Weight | Coating Machine Weight : approx. 2.3t Power Supply Control Cabinet Weight : approx. 2t |
Coating Machine Weight : approx. 3.2t Power Supply Control Cabinet Weight : approx. 2.1t |
Coating Machine Weight : approx. 4.5t Power Supply Control Cabinet Weight : approx. 2.3t |
Coating Machine Weight : approx. 10.8t Power Supply Control Cabinet Weight : approx. 2t |
Option | Shutter for Arc Evaporator Sputter Evaporator |
Dust Booth Shutter for Arc Evaporator Sputter Evaporator |
Shutter for Arc Evaporator Sputter Evaporator |
Shutter for Arc Evaporator Sputter Evaporator |
Typical coating film properties.
Film type | TiN | TiCN | TiAlN | CrN | AlCrN | DLC |
---|---|---|---|---|---|---|
TiN Titanium nitride | TiCN Titanium carbon nitride | TiAlN Titanium aluminum nitride | CrN Chromium nitride | AlCrN Aluminum chromium nitride | DLC diamond-like carbon | |
![]() |
![]() |
![]() |
![]() |
![]() |
![]() |
|
Color | Gold | Gray~Purple | Purple | Silver | Black Gray | Black |
film thickness(μm) | 2~4 | 2~4 | 2~4 | 2~4 | 2~4 | 0.1~20 |
Vickers hardness(Hv25gf) | 1800~2200 | 2000~3000 | 2000~3000 | 1200~2200 | 2000~2500 | 15~70 (GPa) |
Wear resistance | 〇 | ◎High load sliding environment | ◎High temperature cutting environment | ◎High load sliding environment | ◎High temperature cutting environment | ◎Sliding environment |
Heat resistance(℃) | 600 | 500 | 800 | 800 | 900 | 450 |
Processing temperature(℃) | 400~480 | 400~480 | 400~480 | 400~480 | 400~480 | 150~300 |
Application example | General cutting tools General-purpose molds |
Punch/Die Sliding parts |
High-speed cutting tools High-temperature molds |
Machine parts/Engine parts Cr plating alternative |
High-speed cutting tools high-temperature molds |
Machine parts / Engine parts cutting tools |
Film characteristics | general purpose Film | Low coefficient of friction high hardness |
High temperature oxidation resistance | Abrasion resistance heat resistance |
High temperature oxidation resistance | Low coefficient of friction high hardness |
* In addition, the ITF coating machine can coat variety of films depending on the type and Layout of Evaporation source.