What is PVD?
PVD is an abbreviation for physical vapor deposition.
PVD is a method of forming a film by evaporating a solid material by plasma and physically vapor depositing the evaporated material on the coating target.
We customize and sell the Machine that enables film formation by this PVD method according to the customer.
Principle drawings of evaporation
Principle of the arc ion plating method
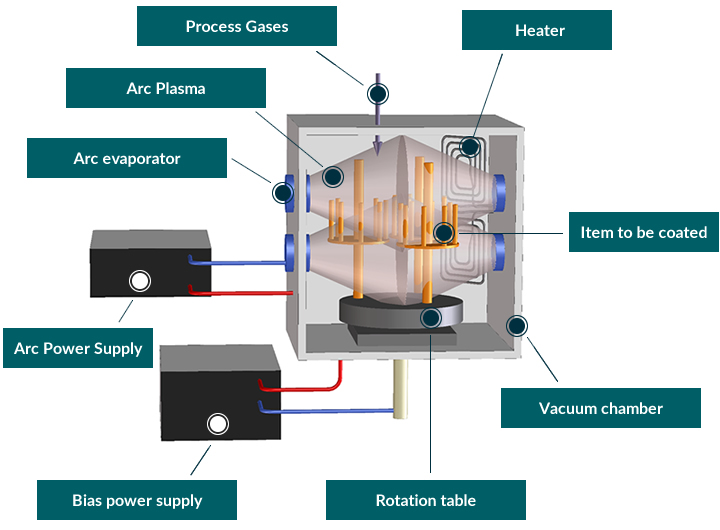
A rotation table with the items to be coated such as a drill, is loaded into the vacuum chamber, and evacuated.
As a first step, items will be heated by radiation heaters, and bombardment step as surface cleaning be taken.
Negative voltage will be applied thru rotation table from bias power supply.
Furthermore by turning on the arc power supply, arc plasma will be taken place at arc evaporator.
The metal material will be evaporated and be ionized by arc discharge, be coated on the items. At the same time, metal atoms are combined with the process gases such as a nitrogen that introduced into the chamber, metal nitride film is formed.
Principle of the sputter ion plating method
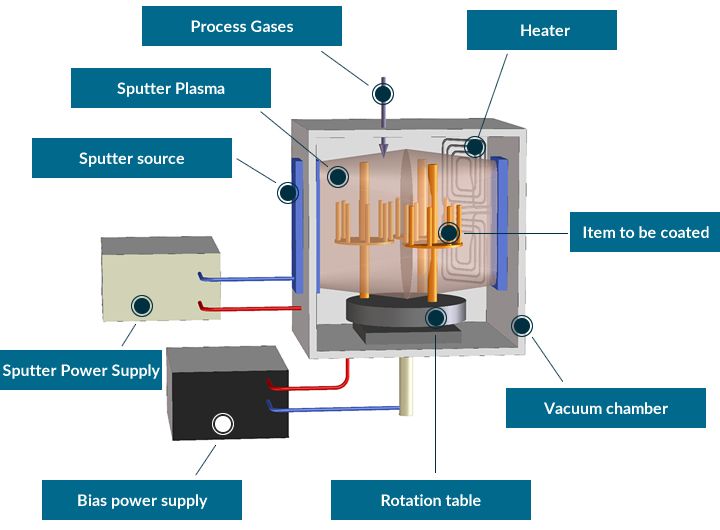
A rotation table with the items to be coated such as a drill, is loaded into the vacuum chamber, and evacuated.
As a first step, items will be heated by radiation heaters, and bombardment step as surface cleaning be taken.
Negative voltage will be applied thru rotation table from bias power supply.
Furthermore by turning on the sputter power supply, sputter plasma will be taken place at sputter source.
The metal material will be sputtered by sputter plasma, be coated on the items. At the same time, metal atoms are combined with the process gases such as a nitrogen that introduced into the chamber, metal nitride film is formed.
Line-up of Arc Evaporator and features
Arc evaporator and sputtering sources are important parts of coating machine.
We have spent many years researching and developing for these.
In principle, the arc method has a problem that coarse particles (droplets) are emitted due to excessive melting of the metal material, but we have developed a technology that can substantially overcome it.
However, it is not "one-size-fits-all", and the optimum method differs depending on the material.
Type of Arc Evaporator | Image illustration | Representative application | Feature of evaporator | Operating range(Arc Current) |
---|---|---|---|---|
2S evaporator | ![]() |
For metal nitride film | Since 2S evaporator can operate with a low arc current, it can be used for low temperature coating (approx. below 200°C). | 40-150A |
2SD evaporator | ![]() |
For multi-layered metal nitride film. | Two cathode materials can be attached to one evaporation source, and either one can be used selectively. In addition to 2S evaporator's advantage, it can be use to for deposition of special multi-layered films by switching alternately two cathode materials . |
40-150A |
3S evaporator | ![]() |
For metal film and metal nitride film. | Less droplet and smooth metal and metal nitride film can be formed in plasma by a strong magnetic field. | 60-150A |
Steer One evaporator | ![]() |
For formation of metal nitride films (especially alloy films) |
For operates at high arc current and is suitable for high speed deposition. It can form smooth alloy film such as TiAl or AlCr. |
100-200A |
Flat 3S evaporator | ![]() |
For formation of hydrogen-free DLC films. | Evaporation source that dedicated for carbon cathodes. It can form DLC film with a high hardness of up to 70 GPa . |
40-150A |
MFA evaporator | ![]() |
For formation of smooth hydrogen-free DLC films. | It is a filtered type arc evaporator for carbon cathodes. | 120-200A |
Sputter source | ![]() |
Formation of smooth metal film, metal nitride film, formation of adhesion layer |
This is an evaporation source that uses the sputtering method instead of the arc method. A smooth film can be formed without droplets. |
Maximum power density 10W/cm² |
We manufacture coating machine
that matches the customer's purpose.
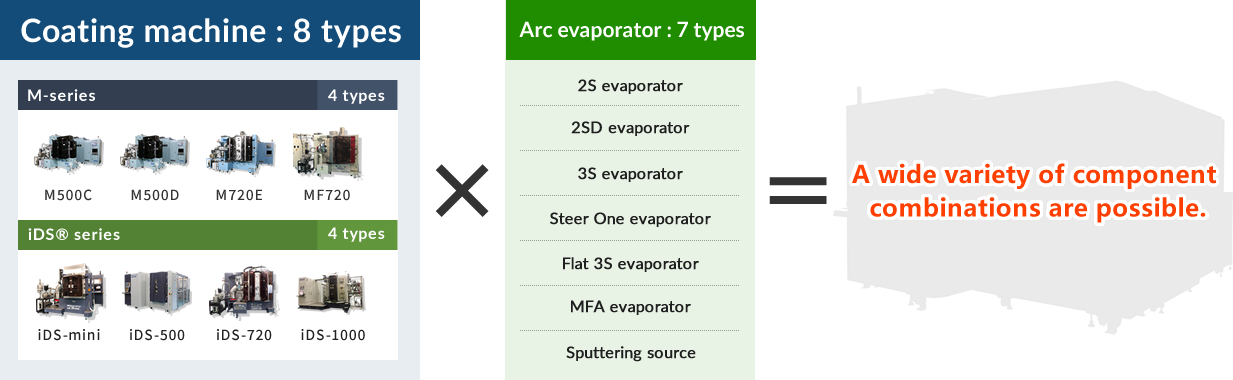
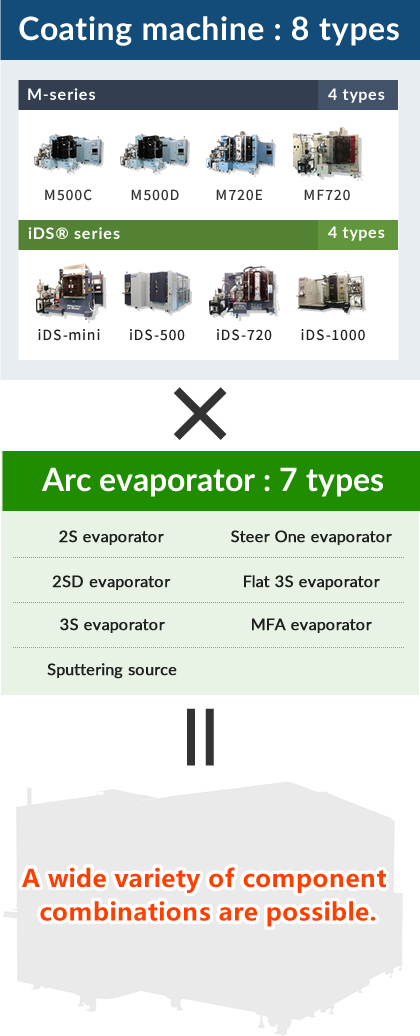
Past combination table of systems and sources
The table shows compatibility of each equipment model in combination with each evaporation source.
The iDS series is suitable with steer-one evaporation sources and sputter sources, while the M series is suitable with other evaporation sources.
Arc evaporator/Coating machine | M500C | M500D | M720E | MF720 | iDS-mini | iDS-500 | iDS-720 | iDS-1000 |
---|---|---|---|---|---|---|---|---|
![]() |
![]() |
![]() |
![]() |
![]() |
![]() |
![]() |
![]() |
|
2S evaporator | 〇 | 〇 | 〇 | × | 〇 | 〇 | 〇 | 〇 |
2SD evaporator | 〇 | 〇 | 〇 | × | × | × | × | × |
3S evaporator | 〇 | 〇 | 〇 | × | × | × | × | × |
Flat 3S evaporator | 〇 | 〇 | 〇 | × | × | × | × | 〇 |
Steer One evaporator | △ | △ | △ | × | 〇 | 〇 | 〇 | 〇 |
MFA evaporator | × | × | × | 〇 | × | × | × | × |
Sputtering source | × | × | 〇 | 〇 | 〇 | 〇 | 〇 | 〇 |
〇:Can be installed
×:Cannot be installed
△:Installation is possible, but some functions are limited.