PVDコーティング(窒化膜)とは
代表的なPVDコーティング(窒化膜)の材料
PVDコーティングで作る窒化物とは、金属が窒素(元素記号N)と化学反応してできた化合物(「遷移金属窒化物」と総称されます)のことを指します。 PVDコーティングにおいて基本となる窒化物は、チタンの窒化物である窒化チタン(化学式TiN、以下TiN)と、クロムの窒化物である窒化クロム(化学式CrN、以下CrN)の二つです。 窒化物は金属の状態よりも硬くなり、一般的な部品材料や工具・金型材料である鉄鋼材料や超硬合金よりもさらに硬く、金属などの相手材と擦れたときに摩耗しにくいというのが最大の特徴です。
窒化物系膜材料を作る方法にはCVD(Chemical Vapor Deposition、化学蒸着)法と呼ばれる方法もありますが、化学反応を起こさせるために1000℃近い温度へと加熱する必要があります。 これに対してPVD(Physical Vapor Deposition、物理蒸着)法は、500℃前後あるいはそれ以下の温度で行われます。PVD法のほうが焼入れ焼戻しされた鉄鋼材料への熱影響が少ないことなどから、当社ではPVDコーティングを採用しています。 それ以外にもPVDコーティングには、膜の特性を制御することが容易で、添加元素の種類や量を調整しやすいといった沢山の特徴があります。
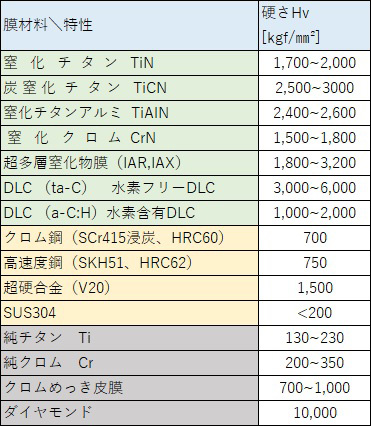
窒化物系膜材料のバリエーション(組成と物性の相関)
主成分となる金属と、炭素・窒素の割合、添加元素の種類や量で変わる材料特性
TiNやCrNに炭素C、アルミニウムAl、シリコンSiといった三つ目の元素を添加することで、硬さ(Hv)や滑りやすさ(摩擦係数)、温度が上がった時の酸化しにくさを変化させることができます。以下具体的な例を挙げて説明します。
窒化チタンTiNへの炭素の添加による膜特性の変化
TiNに炭素Cを添加するとTiCNになり、更に炭素を増やして窒素をゼロにすると炭化チタンTiCになります。炭素の添加量が増えるにつれて、金色だったTiNの色調が次第に茶色、紫色を経て銀色へと変化し、膜硬さHvが2000弱から3000程に上昇し硬くなります。
TiNに比べてTiCNのほうが摩擦係数が小さく、摩耗が少なくなります。
大気中で温度を上げていったときに酸化が始まる温度は、TiNの600℃に対して、TiCNは400℃と、炭素を増やすにつれて低くなります。
窒化チタンTiNへのアルミニウムAlの添加による膜特性の変化
大気中で温度を上げていったときに窒化物系膜が酸化を始める温度が高いほど、切削工具や金型における寿命が延びることが知られています。TiNが600℃以上になると酸化し始めるのに対して、TiNにアルミニウムAlを添加した窒化チタンアルミTiAlN(以下TiAlN)では、900℃まで酸化が抑えられるようになります。
TiNにアルミニウムを添加することによって、耐酸化性だけでなく、硬さが上昇し、膜の色調も金色から褐色、紫色へと変化します。
チタンTiの代わりにクロムCrを使うことによる膜特性の変化
CrNはTiNにおける金属チタンTiの代わりに金属クロムCrを使った窒化物です。
TiN、TiAlNとCrNの硬さと耐酸化性を調べたところ、CrNの硬さはTiNよりも低いですが、耐酸化性はTiAlN並みに優れることが判りました。
以上述べたように、窒化物系膜材料は、主成分である金属の種類・組成と、窒素・炭素の組成比、添加元素の量によって、硬さや耐酸化性といった材料特性が大きく変化します。酸化開始温度を横軸に、膜硬度を縦軸にとって、別のページで紹介しているDLCを含めて各種の膜材料の位置付けをまとめると図1のようになります。
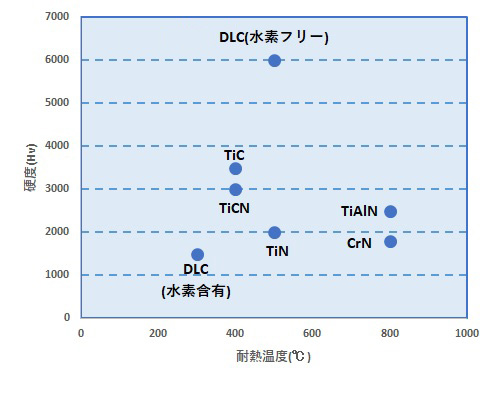
なおDLCは炭素主成分が材料であるために、空気中で400℃以上に加熱されると、徐々に二酸化炭素CO2になって失われてしまいます。DLCを適用できる用途が「温度が高くない環境(目安として300~400℃以下)」に限定される理由が、炭素主成分が材料であるが故の耐酸化性の低さにあります。 しかし、多くの摺動部品は室温から200℃までの温度範囲で使われるため、DLCの耐酸化性の低さが問題になることは余りありません。
図1と表2を参考にして、各種の膜材料(DLCと窒化物系膜材料)を適材適所で使い分けると良いでしょう。選択に悩まれた時はお気軽にお問い合わせ下さい。
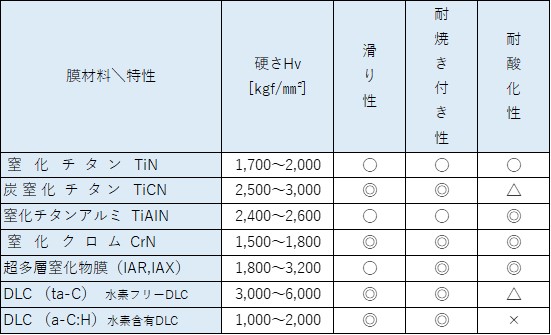
PVDコーティングの特徴
PVDコーティングには、他の表面処理技術やCVDコーティングにはない特徴が他に幾つもあります。それらのうち最も特徴的な点をひとつ取り上げて説明します。
(もうひとつの「圧縮残留応力による部品・工具・金型の疲労強度向上」につきましては詳細版にて解説します)
超多層構造の実現と膜特性の飛躍的改善
PVD法のうちイオンプレーティングに分類される手法は、ホローカソード放電式・電子ビーム式の「溶融るつぼ式」、「スパッタリング式」、「真空アーク放電式」(以下 アーク式)の三つに大別されます。
このうち「スパッタリング式」と「アーク式」は、いずれも「固体の原料の表面から金属を直接蒸発させる」ものであり、真空容器の壁面に複数(2基以上)の蒸発源を備え、「二種類以上の金属を原料としたコーティング」が可能です。 これは「溶融るつぼ式」にはない特徴です。
図3に当社が採用している「アーク式」の装置の模式図を示します。 真空容器中央の自公転テーブルの上に基材保持治具が設置され、コーティングされるようになっています。
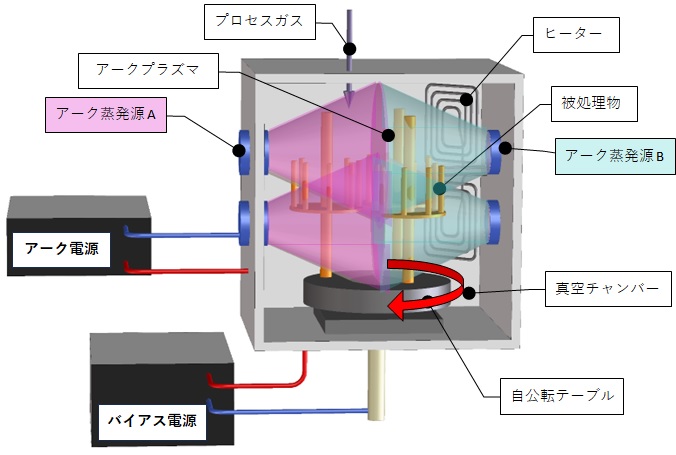
蒸発源から金属を供給しながら基材保持治具を回転させると、蒸発源Aの正面ではAの窒化物が、蒸発源Bの正面ではBの窒化物が、基材表面に交互にコーティングされます。すると、一定時間が経過すると、膜の断面はミルフィーユやバウムクーヘンのような、「Aの窒化物とBの窒化物が積層された構造」になります。
膜が成長する速さと回転速度を調整することによって、異なる二種類の窒化物の積層構造の「積層周期(窒化物Aと窒化物Bの各1層の厚みの和)」を変化させることができます。
二つの異なる材料が積層されるとき、積層周期が「或る値」になると、積層膜の特性が飛躍的に向上する現象が広く知られています。弊社では「窒化チタンTiNと窒化アルミAlNの超多層膜における膜硬さの向上効果」を生かしたコーティング製品を提供しています。
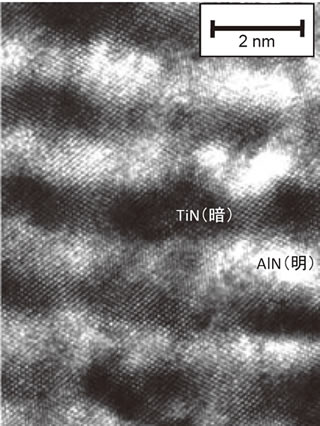
暗層:TiN膜、明層:AlN膜
(参考文献(1)より引用)
PVDコーティングにおける超多層膜の製造方法は、膜への元素添加という観点でも自由度を高めることができます。先程説明したTiNとAlNの組み合わせ(参考文献(1))のほか、TiNとCrN、CrNとAlN、更にはTiAlNと窒化クロムアルミCrAlN(参考文献(2))(以下CrAlN)等、さまざまな組み合わせがすでに実用化されています。
超多層PVDコーティングの登場によって、「耐酸化性がより高く、硬さがより高い膜材料」を作ることが可能になりました。上で紹介した図1「各種の膜材料の材料特性マップ」は、次に示す図4のようになります。
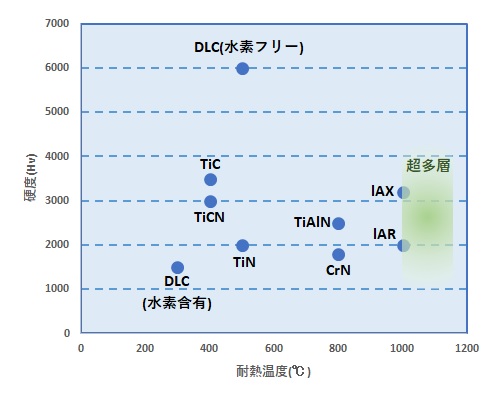
PVDコーティング(窒化膜)のメリット
PVDコーティング(アーク法・ホローカソード法・スパッタリング法)のメリット
低温でコーティングできることや、超多層膜が形成可能なことを記しましたが、これ以外にもたくさんのメリットがあります。対抗技術である熱CVD法と比較したときのメリットを記します。
成膜温度が低い
- 熱CVDと比較し、成膜時の処理温度が低温(500℃以下、熱CVDは約1000℃)。
スパッタリング:約150℃~ < アーク:300℃~500℃ < ホローカソード法:約500℃ - 低温(焼き戻し温度以下)での処理のため、熱変形(変寸)や熱変質(焼き鈍り)のリスクが低く、薄膜処理のため精度の厳しい製品への処理も可能。
- 除膜+再コートが容易
原料選択の幅が広い
- 固体原料のため様々な元素構成の膜を作ることができ、膜構造も単層・積層・超多層の膜を作ることが出来る。それにより必要な機能付与が出来る。
安全性が高い
- 熱CVDのような危険なガス(塩素ガス、水素ガス等)を使用しない。
製品への最終処理のため、直ぐに使用できる。
- 熱CVDは処理後に、再熱処理やショットピーニングが必要となる。
被膜に圧縮残留応力を付与し制御することができる。
- 欠けや折れ、割れ等を抑制し疲労強度の向上が図れる。
熱CVDとPVD比較表(参考)
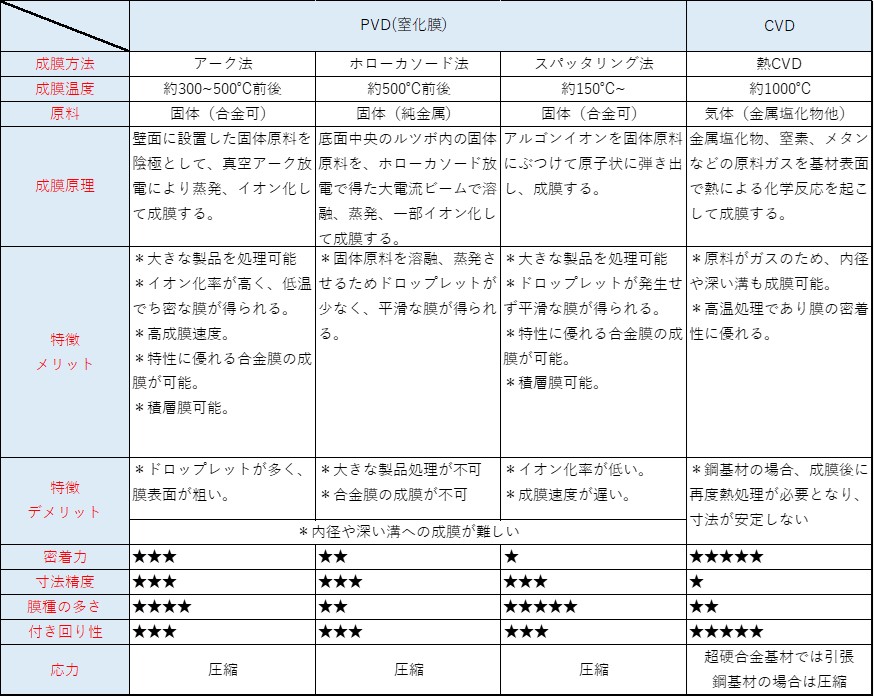
窒化物系PVDコーティングの産業的価値
窒化物系PVDコーティングは環境に優しい技術
高硬度(耐摩耗性に優れる)
- 部品の寿命延長 → 廃棄物の削減、省資源化
- 再コーティングによる再生 → リサイクルの推進
- 部品の軽量化 → 省電力化
低摩擦係数(摺動性に優れる)
- ドライプロセスの実現 → 潤滑油の削減、洗浄処理の削減
- 凝着防止 → 高面圧環境でのかじり防止
- 摩擦熱の抑制 → 工具や加工対象物の熱劣化の防止
化学的不活性
- 凝着・溶着の防止 → 生産性向上、工具・治具のメンテナンス軽減
- 相手材の変質防止 → 仕上げ精度の向上
耐食性
- 腐食劣化の防止 → メンテナンスの負荷軽減、部品の寿命延長
弊社では、様々な経験を素に、お客様の課題に応じた窒化物系PVDコーティングを提案いたします。是非、ご相談ください。
信頼性に優れた表面処理を提供するPVDコーティング
装置開発技術とプロセス技術を融合し最高の窒化物系PVDコーティングを提供
窒化物のPVDコーティングが世に広まった1980年代には、PVDコーティング製品の品質や性能が不安定となる場面も多く発生しました。特に基材との密着力と、膜の平滑性が大きな課題でしたが、装置開発技術とプロセス技術の改良により改善し、適用分野がますます広がっています。
高性能なコーティング膜の形成を可能にする装置
弊社が採用しているアーク式のイオンプレーティング法は、高いイオン化率により密着性に優れたコーティングを形成できる特徴から、工具・金型などの用途で適用されてきました。 しかし蒸発材料表面にアーク放電を起こした際に飛び出す数十~数百ミクロンのサイズの金属粒子(ドロップレット・液滴)により表面の平滑性が低下する課題がありました。 その抑制のためにアーク蒸発源のガス供給機構や磁場制御の改良が進められてきました。具体的には窒素ガス環境下でアーク放電を起こし金属材料の蒸発を高融点化させることや、カソード裏面で永久磁石を回転させアークスポットを強制的に掃引することでドロップレットの低減が図られています。 弊社では、これらの最新技術を搭載したコーティング装置の製造販売を行っています。(参考文献(3))
蒸発源以外でも、基材に付着している水分などを離脱させる加熱真空排気機構や、基材表面のエッチングガスボンバードユニット機構を設置し、密着力の高いコーティング膜の作成を可能にする工夫がなされています。
弊社では他にもターゲット寿命の延長、成膜レートの低下抑制にも配慮し、より低コストで操業可能な装置を提供し、お客様に喜ばれるよう日々研究開発に取り組んでおります。
最高の性能を引き出す前後処理技術
現在では、成膜プロセスはもちろんのこと、成膜前に行う基材洗浄プロセスについても数多くの新技術を開発・導入し、基材表面の清浄化、膜特性の制御・適正化ノウハウを蓄積してきており、膜の密着性、長期の安定性、靭性が向上し、十分信頼できるものとなっています。 成膜プロセス中の設備の挙動も従来以上に詳しく記録・解析できるようになり、異常発生時の原因調査・解析が行えるようになりました。そして切削性能等の製品性能評価も日常的に行っています。
このような背景のもと、切削工具、金型、産業機械や自動車の部品の多くに窒化物系PVDコーティングが次々と採用され、世の中の全てのものづくりにおいて窒化物系PVDコーティングは無くてはならない存在となっています。
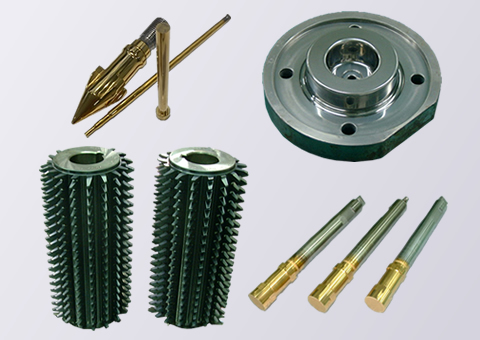
評価分析技術で安心できる膜を提供
窒化物系PVDの成膜技術とともに、信頼性の後ろ盾となっているのが、膜の評価分析技術です。
実際に成膜した窒化物系PVDコーティングの耐久性や機能性を、摩耗試験や剥離試験、耐熱試験、切削性能試験といった様々な要素で検証し、その結果を分析します。
もし、少しでも合格基準に満たない要素があれば、直ちに膜の組成やプロセスを改良し、新たな膜を開発して、再び検証を行います。
このような評価に関する「設備・技術・ノウハウ」を保有していることも、窒化物系PVDコーティングに責任を持っておすすめするサプライヤーの務めだと考えています。
窒化物系PVDコーティングの用途
新たな分野へ広がる、窒化物系PVDコーティングの利用
窒化物系PVDコーティングは、様々な分野で注目されており、今でもなお研究開発が進められていることはもちろん、すでに数多くの用途で実用化されています。
今、取り組んでいる開発で、あるいは工場のものづくり改善で、窒化物系PVDコーティングを活用してみたい。というお考えがあれば、是非当社までご連絡ください。条件に合わせた膜種やプロセスをご提案し、試験成膜や評価等のご協力もさせていただきます。
切削加工分野
- 切削工具(ドリル、エンドミル、バイト、刃先交換型工具の刃先チップ、リーマ、メタルソー、ホブ、ピニオンカッタ―、ブレード等)
- スリッター、チップソー
金型分野
- 冷間・温間・熱間鍛造金型
- プレス金型(曲げ・絞り・打ち抜き、ファインブランキング、せん断)
- 樹脂成型金型(インジェクション、射出、押出し、ブロー、圧縮、真空、Tダイ)
- ゴム成形金型
- ガラス成形金型
- ダイカスト金型(普通、高真空、スクイズ、半溶融・半凝固、PF)
- 容器加工用金型
OA機器分野・機械部品分野
- 摺動部品(ローラーシャフト、クランク、ジョイント、スライダー、軸受け)
- 動力伝達部品(ギア、プーリー、減速機)
- ギアポンプ部品
自動車分野
- エンジン部品(給・排気バルブ、ピストンリングなど)
家庭用品、建築
- 包丁、はさみ、剃刀
各種用途に関する詳しい内容は、弊社営業窓口までお問い合わせ下さい。
様々な経験を素に、お客様の課題に応じた窒化物系PVDコーティングをご提案させていただきますので、是非、ご相談ください。
(このページでは、硬さHvの単位はkgf/mm2とさせていただいています。Hv単位の硬さをGPa単位に換算する場合は102で割ってください。 本解説で記載の特性値は一般的なPVDコーティングの値を記載しています。組成や成膜プロセスにより特性値を調整することもできます。)
【参考文献】
(1)福井、「切削工具用コーティング技術の進化 ~CVD法とPVD法~」、SEIテクニカルレビュー、第188号、2016年1月、p.26-31
(2)瀬戸山ほか、「最近の切削工具用PVDコーティング膜」、高温学会誌 2007 年 33 巻 2 号 p. 90-94
(3)岡崎、「コーティング装置とその要素技術の変遷」、日新電機技報 Vol. 62, No. 3(2017.10)